Aeronautics
Carbon fibre is the strategic material for the aeronautical and space industries of the future.
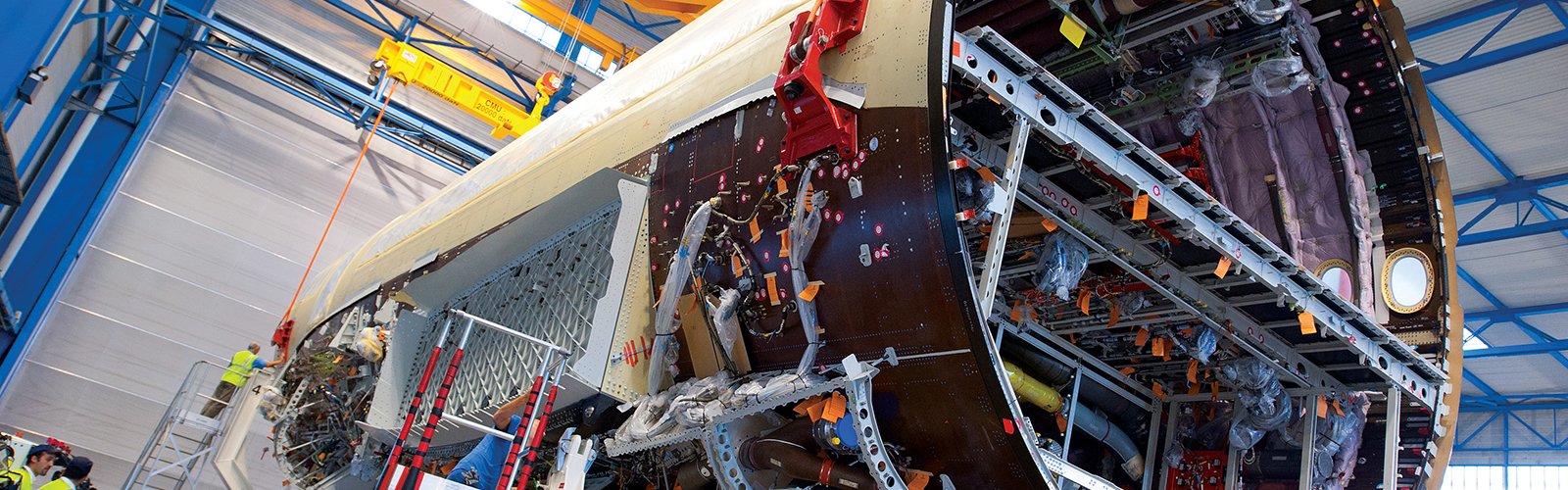
Flying further, but consuming less fuel
Carbon represents more than half of the structural mass of commercial airplanes
Composites are present everywhere: in fuselage sections, wing panels, air entries, motor blades, empenages, bulkheads… As resin-impregnated carbon fibre or plastic sandwich beams and metallic alloys, these modern materials represent more than half of the structural mass of recent airplanes, such as the Airbus A350 and the Boeing 787. The demand for carbon composites in the aeronautical industry has taken off in the last ten years and will most likely double from now to 2020. Lighter aircraft will evidently fly further and faster, whilst consuming less fuel and therefore contributing to the reduction in greenhouse gas emissions. Additionally, carbon fibre is not susceptible to corrosion and fatigue, so improving aircraft maintenance and reducing inspection intervals.
We are proud to be a second-tier supplier to Airbus
For more than ten years, Heol Composites has produced carbon fibre components as a second-tier supplier to Airbus. These include assembly templates (for example passenger luggage compartments) or drilling templates (in partnership with an aeronautical machining company to guarantee the high precision needed for carbon parts, which do not have the same thermal expansion as the aluminium templates in use today), sample parts to calibrate tooling, test parts (which are sometimes tested to breaking point) or real size demonstrators.
Like the big players in the aeronautical industry, we demand a high standard of quality.
Expertise in the most advanced technologies for unfailing quality
We have also produced hundreds of critical aeronautical parts for amateur built light aircraft (two-seater aircraft Gaz’aile, microlight Luciole….). On these wing beams and landing gear, total reliability is of course the standard, the pilot’s lives depend on them. Our expertise in industrial processes allows for perfectly controlled repeatability. We are setting up a quality management system and are currently working towards ISO9001 certification with a view to obtaining EN9100 in the medium term.
Aeronautical Class 3 certified autoclave, prepregs and carbon infused moulds
In the ocean racing domain, we were amongst the first to use cutting edge aeronautical processes, with the carbon/epoxy prepregs and autoclave pressure curing. Our autoclave is certified aeronautical class 3 (temperature homogeneity of ±3°C). We are very familiar with the fabrication of carbon moulds and tools in resin infusion from machined plugs. These moulds are required to be air-tight and to have perfect geometry to enable the build as per our autoclave technology. We already allow the big players of the aeronautical industry to sub-contract the moulds and demonstrators, before obtaining quality certificates, which are obviously required when building aeronautical parts.
Suivez Heol Composites sur les réseaux