Les pré-imprégnés carbone, notre matière première
Généralement épais de 0.3mm, les tissus en fibres de carbone pré-imprégnés d'époxy garantissent résistance mécanique et légèreté à nos pièces creuses
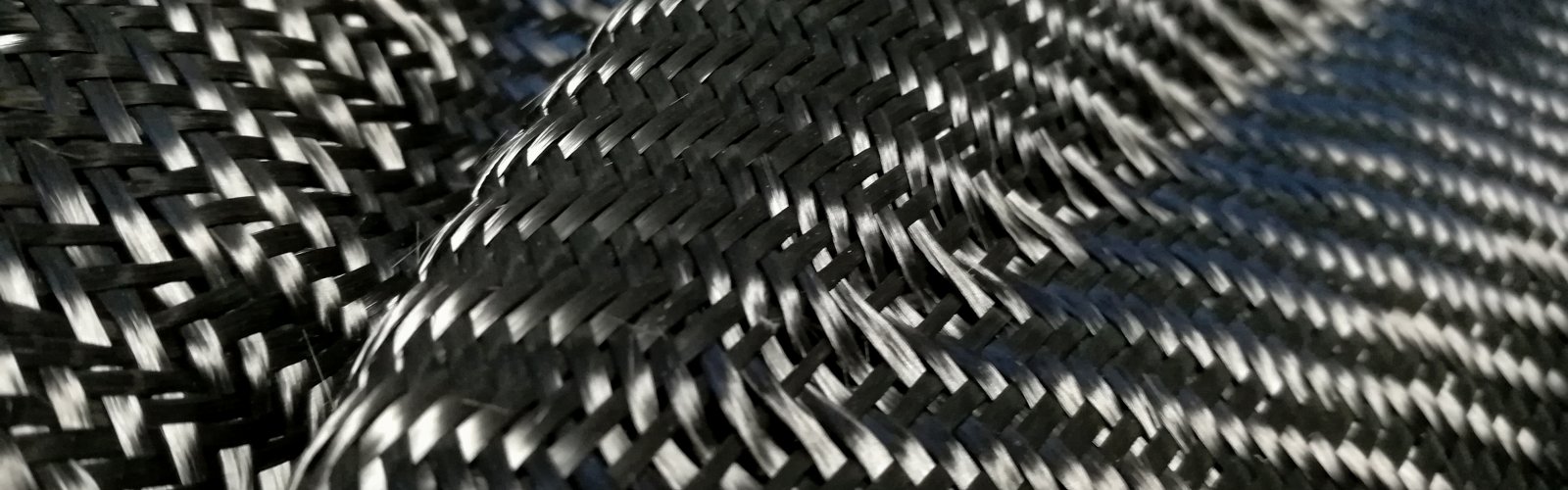
Petite explication sur la fibre de carbone, sa mise en oeuvre et nos brevets d'invention...
Le carbone est notre matière première
Sa fibre extrêmement fine de l’ordre de la dizaine de micromètres de diamètre est fabriquée à partir de la carbonisation d’un précurseur chimique (polyacrylonitrile PAN). L’essentiel vient du Japon, des USA, de l’Allemagne et de la Chine, mais le japonais Toray fabrique aussi en France et l’américain Hexcel y construit une usine.
La fibre est composée d’atomes de carbone qui sont agglomérés dans des cristaux, eux-mêmes alignés parallèlement à l’axe long de la fibre. Cela la rend extraordinairement résistante. Des milliers de fibres sont enroulées pour former le fil qui est ensuite tissé selon différentes orientations (nappe unidirectionnelle, biaxiaux à ±45° et 0/90°, tri voire quadriaxiaux) puis imprégné de résine époxy. Couramment, les nappes présentent un grammage de 50g/m² à 1600g/m² et sont livrées en largeur allant de 25mm à 1600mm.
Nous recevons ces pré-imprégnés en rouleaux de plusieurs dizaines de kilogrammes et de mètres carrés. Nous veillons à la traçabilité de la matière utilisée ainsi qu’à son stockage dans une chambre froide à moins vingt degrés centigrades. En fonction des contraintes mécaniques de la pièce à fabriquer, nous calculons un échantillonnage et établissons un plan de drapage combinant différentes orientations de fibres et épaisseurs. Parfois, certaines pièces très spécifiques sont fabriquées sur des plans fournis par les clients qui réalisent ou sous-traitent les calculs. Pour le grammage le plus couramment utilisé, un pli fait seulement 3 dixièmes de millimètres d’épaisseur. L’opération de drapage dans les moules nécessite donc beaucoup de minutie et de rigueur, afin d’empiler les plis conformément aux calculs de charge.
L'art du drapage et de la polymérisation sous 7 bars de pression
Nous drapons dans des moules femelles demi-coquilles. Les moules sont, soit usinés dans une plaque d’aluminium, soit fabriqués par nos soins à partir d’un modèle en planches usinables selon une technique d’infusion de tissus de carbone secs. Les moules doivent être parfaitement étanches pour résister à la pression de l’autoclave. Nous avons aussi quelques secrets de fabrication en la matière.
La future pièce dans son moule est placé dans l’autoclave où elle va cuire jusqu’à cent vingt degrés et sept bars soit une très forte pression qui va en renforcer les propriétés mécaniques. Comme les recettes des grands chefs, nos procédés de cuisson à l’autoclave ont été patiemment optimisés et sont très confidentiels.
Notre procédé innovant pour la construction de pièces composites en carbone est protégé par des brevets en instance
Notre procédé pour les pièces creuses mono process renforcées par des bandes de cisaillement pour une répartition parfaite des charges est protégé par 2 brevets. Ce procédé exclusif et polyvalent permet la production de pièces structurelles sans aucune limitation dans la géométrie de la forme. Les pièces creuses sont plus légères et nécessitent moins de carbone, qui est un matériau coûteux. La construction one-cure optimise la résistance des pièces et permet une amélioration marquée de l’apparence esthétique. Cela évite également le besoin d’usinage après moulage et réduit ainsi la poussière de carbone générée par les méthodes traditionnelles.
Les pièces obtenues présentent d’excellentes propriétés mécaniques, notamment en traction et en compression, et peuvent être jusqu’à six fois plus légères que les pièces en acier pour une résistance équivalente. En effet, la densité d’un composite époxy carbone est de 1,5, contre 7,8 pour l’acier (donc 7,8 tonnes pour 1 mètre cube). Cependant, le coût est différent et il nécessite de repenser toutes les fonctions de la pièce, dans une analyse de la valeur, ou une refonte axée sur les coûts.
Les pièces fabriquées par Heol Composites depuis 2002 ont été utilisées pour une variété d’applications et dans des domaines très différents (voile de compétition, course automobile, aéronautique, industrie) à la grande satisfaction de nos clients.
Suivez Heol Composites sur les réseaux